
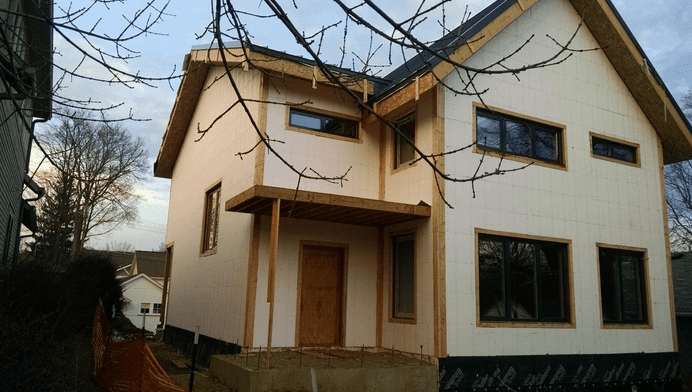
Cedar Street Builder’s InSoFast Application
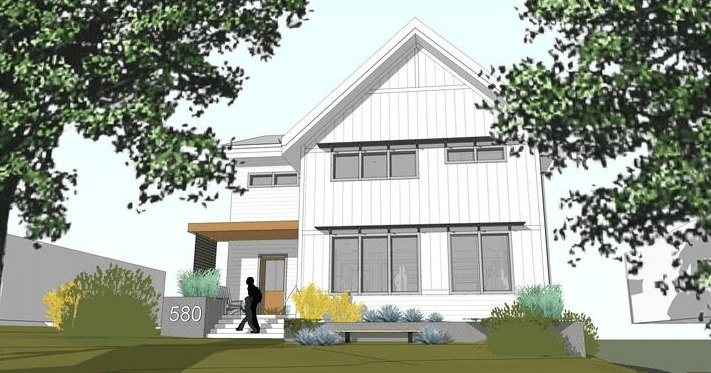
Although code minimums vary from state to state,
InSoFast FP-2.5NRW‘s R-10 capabilities fit the bill in terms of meeting the energy codes for most projects. We’ve also made our panels adaptable with the InSoFast PLUS option, just in case you’re determined to go above and beyond the minimums.
That is exactly what a recent customer has done in a home that required a total of R-52! Yep, that’s not a typo… R-52.
The house dubbed ‘Project 580’ was developed by Dan Porzel of Cedar Street Builders who chose to use our EX panels as one of many insulation components in the Passive House project outside of Indianapolis.
According to the Passive House Institute, “Passive building cuts energy consumption by 60-80 percent compared to code buildings. Certified passive buildings provide superior comfort, indoor air quality, and resilience” with an emphasis on maximizing your gains and minimizing your losses. This involves utilizing continuous insulation methods. InSoFast gives a thumbs up to that!
So we took the time to chat with Dan about this unique InSoFast project and to pick his brain about the Passive House approach.
Tell us about your company.
Cedar Street Builders is a small custom home builder based in the Indianapolis area. We specialize in building high performance homes. This means we put a lot of time and effort into thinking about how the home is built and what new technologies and building methods can be utilized to increase the performance of the home. We think about how these factors will affect the end product in terms of things like monthly utility bills and overall home comfort level.
So you recently used our EX 2.5 panels for a Passive House project in Zionsville, Indiana. You’ve named it Project 580. Can you talk about the inception of this project and how InSoFast came into play?
It’s a house that we actually built for my own family. We wanted to keep the house size and footprint reasonable by utilizing the space well and by editing out any spaces within the house that would end up unused. Throughout our planning of the project I was personally learning more and more about Passive House. I was interested in the challenge of building such a well insulated and air-tight structure. We were searching for the benefits of having low utility bills and an overall comfort to the home, along with simply minimizing our carbon footprint.
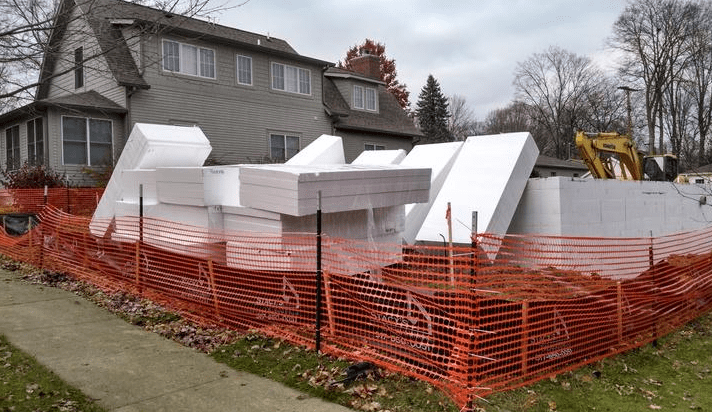
So through our Passive House consultant we were able to get the numbers on what our insulation levels needed to be at for this area. We planned to use SIPS (Structurally Insulated Panels) for the homes enclosure and exterior walls, as well as the roof. I was interested in the SIPS ability to get a nice continuous insulation level and it’s prefab nature which would eliminate some of the onsite waste. Based on our designs, we figured out that the exterior wall would need to have an R-value of 52. The SIPS panels with 10 in thick walls would get us to R-40. We were looking for an addition of about R-10.
We could have possibly used a 12 inch panel (the roof used this panel) instead of the 10 inch, but the costs would have increased quite a bit. We were looking for an alternative way to add another layer of insulation on the outside of the SIPS. Even though the SIPS panels are very continuous they do have some studs that bridge from front to back around windows, so we liked the idea of adding another continuous layer of insulation to kind of wrap the SIPS structure in a nice warm blanket. We also were attracted to the idea of having a rainscreen system within the exterior in order to get some air behind the siding to let the exterior breathe a little bit.
I coincidentally came across InSoFast right when we were thinking about how to accomplish this extra layer of rigid insulation. I believe I first read about the product on Green Building Advisor. InSoFast allowed us to check the continuous insulation and rainscreen system off the list. The plastic studs also made it easier for us to fasten the siding to the panels. So we chose to use it.
It was your team’s first time working with InSoFast. Did the installation run smoothly?
Yes, it was our first time. But we talked about the process beforehand and watched some of the videos from your website. It went really well. We didn’t have any issues- the panels were easy to cut and overall it went in nice and easy. We moved into the house about three weeks ago and it’s feeling good.
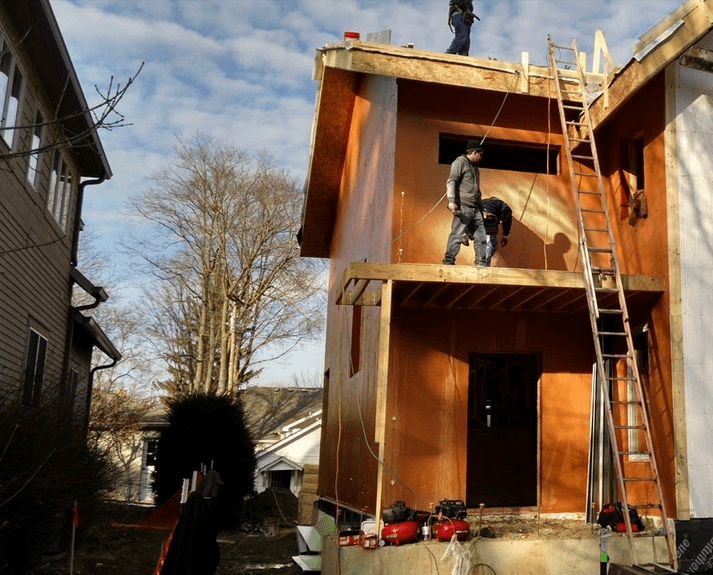
Can you talk about what it means to build a Passive House?
Passive House Building involves trying to achieve a super insulated and air-tight structure. Certain products like very high-performance windows are utilized to help seal the home and achieve a high level of comfort. There are certain guidelines that Passive House Institute mandates that you have to meet in order to reach the Passive House status. There’s an air leakage requirement along with an energy usage requirements for heating and cooling and an overall site energy usage limit. Passive House goes above and beyond code. It goes above and beyond any other building program, whether it’s a high performance or green building program. It aims to really just minimize the energy that is used throughout the life of the home. The idea is to put the effort forward with the structure and how it’s built so that the home will reap the benefits for the next however hundred-long years.
So what other Passive House standards were implemented into the plan of Project 580, besides super insulation?
The most important thing is making sure you have a nice continuous air-seal. You need to kind of draw a line around the whole building and follow one component to the next, so that they all tie together.
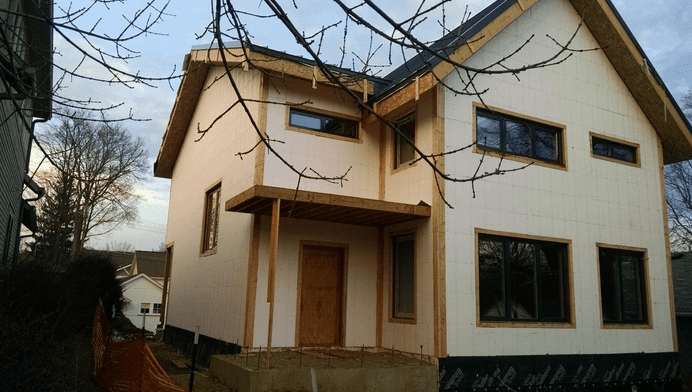
We had the under-slab and a plastic vapor air barrier. Instead of just letting that barrier lie flat you need to make sure it ties into the the next portion of the air barrier which is in the foundation walls. We constructed our foundation walls with ICF’s (Insulated Concrete Forms), which is a very similar product to the InSoFast, since they provide insulation and a continuous air barrier. We paid great attention to the details of how the SIPS Panels lined up with the ICF’s below and how the InSoFast panel lined up with the whole system.
So basically we set the SIPS panel 2.5 inches inside of the ICF’s so that the InSoFast panel would line up nicely with the outside of the ICF. The air and water barrier we used on the outside of the SIPS panel was a very high performance liquid applied membrane. It was rolled on instead of using a paper barrier to provide a continuous barrier on the outside of the SIPS. We also put another 8 inches of insulation underneath the basement slab.
As R-values increase there is a diminishing return of the amount of energy saved from added insulation. In your opinion what makes it worth it to ‘super-insulate’ in the way that is typical of Passive House design?
The most important thing is getting to the point where you can achieve your heating and cooling with a certain mechanical design that doesn’t require the traditional furnace. In order to get to that level and be confident that it’s going to keep the whole house comfortable you really do have to go to some of these extreme levels with insulation. We do have two mini Mitsubishi mini split heat pumps, as well as our ventilator that keeps bringing in fresh air into the house. You could probably achieve some really good results with a lot less insulation, but you can’t get to that point of minimizing your use of mechanical systems the way that we have.
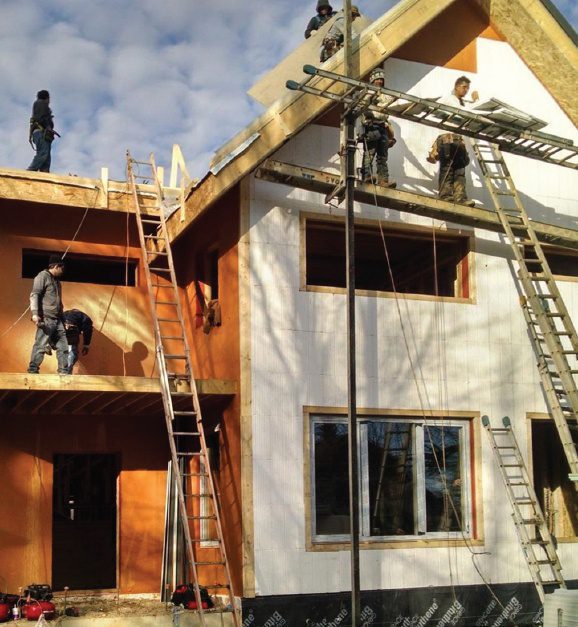
Dan Porzel is a graduate of Bradley University’s Construction Engineering & Management program, a LEED AP, and brings 15 years of working in a collaborative construction environment pursuant of the highest quality construction achievable. Dan has completed multiple LEED (US Green Building Association’s green building program) Certified projects and had become a proponent of the IPD (Integrated Project Delivery) and LEAN Project Design & Construction methods.
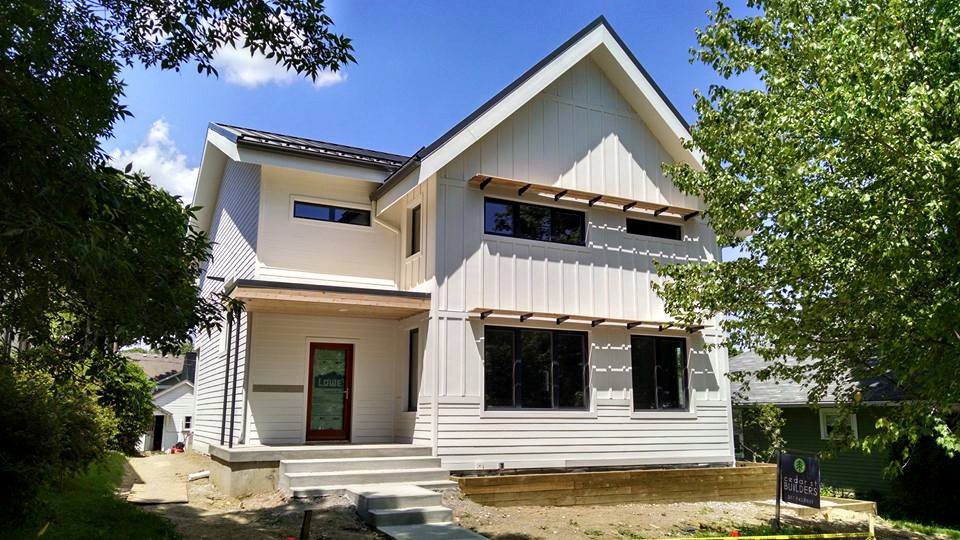
Dan has also been recently trained in Passive House building methods by the Passive House Institute US. He continues to use his diverse background to build the next generation of custom homes with Cedar Street Builders.
Thanks for taking the time to speak with us Dan!